GUIDE TO YIXING TEAPOTS
How To Tell a Fake
About
Due to the nature of Yixing pottery's unique construction method there are some very distinct features that authentic pots will carry. The pots are built from slabs of material then joined together almost akin to a gingerbread house. This is very contrary to wheel thrown, slip cast, or machine molded pottery. The surface should have little black dots: Tierong 铁熔, tiny white dots: Yunmu 云母, tiny divots: Tiaosha 跳砂, and finally tiny bumps: Baozi 爆子. Below are more visual and tactile give aways for identifying authentic Yixing ware. They will go from easiest to spot to more nuanced details. It should be noted that Factory made pots (I.E. pots produced by Yixing Factory one) do not follow these rules at all. Factory pot authentication is an entirely different entity.

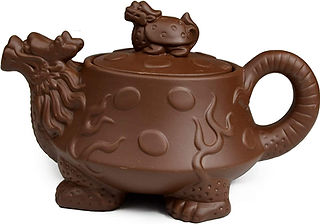
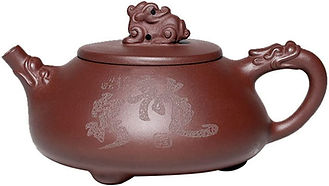


Overall Design
Off the bat, if you come across a pot that is made to look like an intricate tree stump with blossoming flowers and a handle imitating natural bamboo. It's fake. 99.99% of pots are very plain and straight forward designs (see the "teapot shapes" page). The only exception to this is handmade masterworks where artists are trying to make artful boundary breaking pieces. These will not be sold anywhere where you can acquire them for less than an arm and a leg. Here are some examples of over the top designed fakes. All of these pots are listed for below 70 USD. They are, without a doubt, mass molded pots produced from generic clay.

底片、满片
Top and Bottom Seams
The body of Yixing teapots are (in a very reductive explanation) made in three pieces. You have a flat slab of clay cut to shape as the bottom. To that bottom you take a long rectangular sheet of clay and wrap it around to form the walls of the pot. Then you top it off with another slab of flat clay. The transition between these pieces will have a different grain much like wood. The seems should be visible at the lip of the pot and the bottom edge. Slip cast pots will never have this. Keep in mind some pot shapes have slightly different construction and will do this differently but for 90% of pots you should see these. The picture shows a very obvious bottom seam or 底片. Note it will almost never be this obvious. Usually you have to shine some light on it. Hand made pots will always have both. Half handmade can have both or just the bottom.
推墙挂底
Internal Tooling Marks
To make the internal chamber of the teapot, the base has to be worked ands joined to the walls. A bamboo tool is used to move clay outward from base to wall radiating from the center of the base. These lines should be straight and only go a small amount up the walls. This is however often done to slip cast pots to make them seem more authentic.

Spine Seam
The walls of the teapot are formed from one sheet of clay wrapped around on itself and blended. However the seam where the two ends meet is often still visible and at the very least can be felt. The picture displays a very prominent spine seam. Most I have encountered are not easily seen.

Felt But Not Seen
There are a couple more tips off to the authenticity of a pots construction that can not be seen in photographs. The most obvious one is feeling the under side of the rim of the pot opening. A string of words, I know. But you are looking to feel a hard, often rough, edge under the pot opening before it transitions to the inner walls. Additionally when the lid meets the body with a light tap or being rubbed, the sound should be high pitch like porcelain. There should be no dust, flakes, or color that transfers to your hands upon touching an authentic teapot.